Un po' di storia del circuito stampato...
Il PCB dagli anni '50 ad oggi
Il circuito stampato (detto anche PCB, acronimo di printed circuit board) ha oramai oltre mezzo secolo di storia alle spalle in Italia, dato che la sua storia, nel nostro Paese, ha avuto inizio verso la fine degli anni '50: a questo periodo risalgono infatti le prime realizzazioni di circuiti stampati monorame per applicazioni in campo elettromeccanico.
A quei tempi venivano usati laminati per circuiti stampati in bachelite (che successivamente prese il nome di 3XPC). I disegni delle piste su questi circuiti venivano stampati con il metodo della serigrafia, e l'incisione del rame avveniva utilizzando cloruro rameico, cloruro ferrico o miscele solfo-cromiche; i fori venivano eseguiti per tranciatura, assieme al contorno, mentre la protezione delle piste (al fine di evitare l'ossidazione) avveniva con una soluzione acquosa o alcoolica di pece greca (colofonia) la quale aveva anche un'ottimo potere flussante al momento della sublimazione in saldatura.
Dai primi anni sessanta incominciò in Italia la produzione dei primi circuiti stampati doppia faccia, caratterizzati da fori passanti metallizzati (Plated Through Hole); questi circuiti stampati erano realizzati su laminati di fibra di vetro impregnati in resina epossidica detti G10, o più comunemente vetronite (l'attuale FR4); questi PCB venivano anche detti circuiti stampati professionali, per differenziarli dai circuiti stampati monofaccia che venivano invece classificati come civili.
I circuiti a fori metallizzati erano realizzati sempre con stampa serigrafica ma in negativo, e solamente dopo la metà degli anni sessanta si iniziò ad utilizzare fotoresist liquidi sostituiti dopo breve da dry film. Il processo di metallizzazione dei fori avveniva per deposizione chimica di rame disciolto nei sali di Signette (tecnologia nota da secoli, perchè si tratta della stessa che consentiva di depositare palladio e rame sul vetro per fare gli specchi); i fori così metallizzati venivano successivamente rinforzati con con un procedimento galvanico in una soluzione di solfato di rame. Le piste venivano a questo punto ricoperte di stagno puro (stagno Culmo, che appariva lucido) oppure in stagno/piombo (che appariva opaco e scarsamente saldabile); tali rivestimenti avevano anche la funzione di Etching resist, ossia di resistenza all'incisione, e resistevano ad un bagno di acido solforico e acqua ossigenata, persolfato di ammonio o soluzione cuproammoniacale che servivano per rimuovere il rame non protetto lasciando solo le piste e i fori metallizzati. Nel caso di circuiti prodotti con stagno/piombo (SnPb 63/37) era necessario un procedimento termico detto rifusione o surfusione che rendeva la superficie perfettamente saldabile: questi trattamenti avvenivano inizialmente immergendo i circuiti stampati in un bagno di olio bollente a 240°C.
Verso la metà degli anni settanta comparvero in Italia i primi forni per rifusione ad infrarossi, del tutto simili ai forni per la saldatura di componenti SMD. L'esigenza di limitare le aree di saldatura del circuito stampato nacque verso la fine degli anni sessanta impiegando appunto solder resist stampati in serigrafia, che normalmente avevano colore verde. Nello stesso periodo negli Stati Uniti iniziarono le prime produzioni di circuiti stampati multistrato, ovvero con piste di rame anche tra gli strati di fibra di vetro interni al laminato. In questo modo i fori metallizzati intercettavano le piazzole di rame degli strati interni e aumentavano quindi il numero dei collegamenti possibili. Questa tecnica è quella che ha consentito di iniziare la corsa all'integrazione per produrre circuiti stampati sempre più complessi e con una densità di componenti sempre più vicina al 100% della superficie disponibile.
Circuiti stampati Baselectron
Vai alle schede prodotti
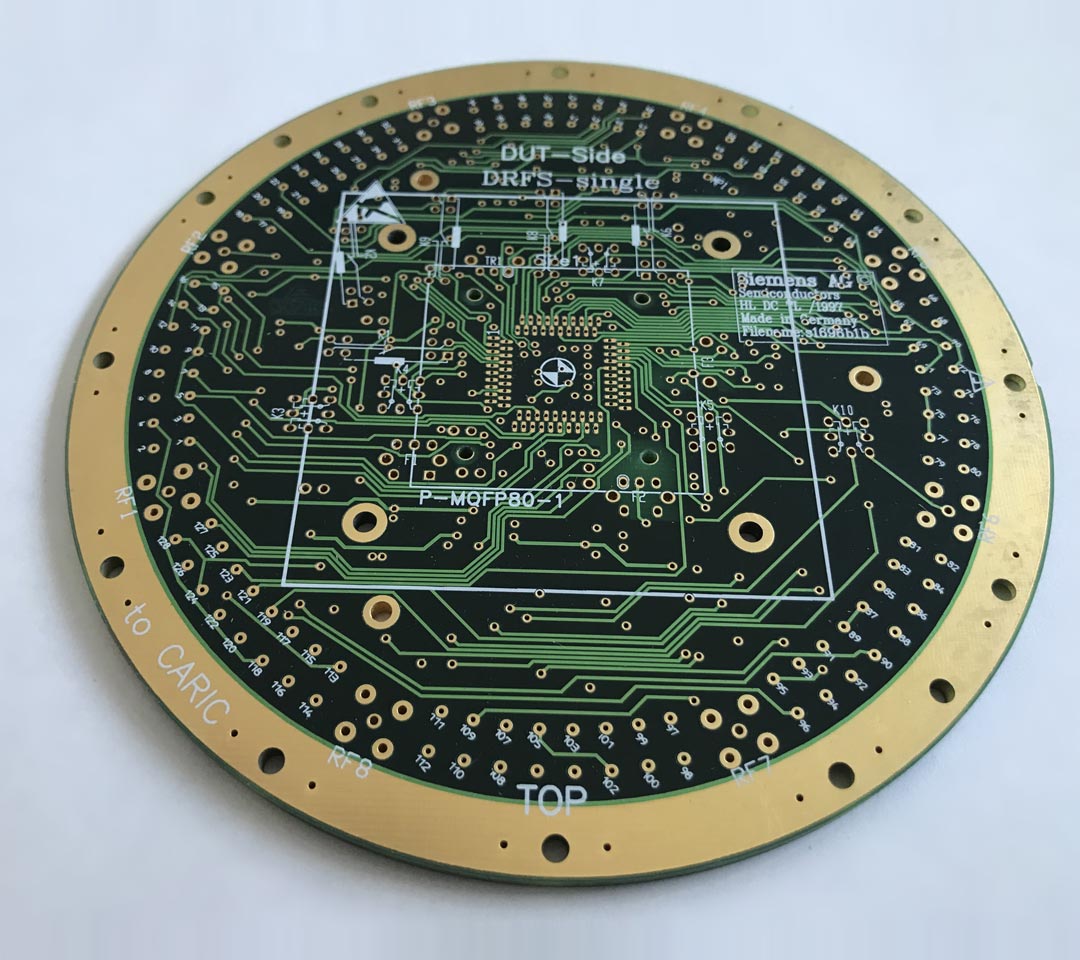
Nota:
I circuiti stampati sono anche chiamati in modo differente in funzione delle loro caratteristiche, ad esempio:
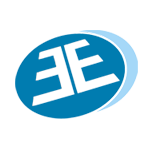
Singola faccia
Monofaccia, Monolayer, Single side e Monorame sono modi diversi per identificare un circuito stampato a singola faccia ovvero con un solo strato di piste.
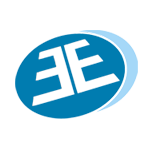
Doppia faccia
Doppiolato, Bilayer, Double side e Doppiorame, sono modi diversi per identificare un circuito stampato a doppia faccia ovvero con le piste su entrambe le superfici.
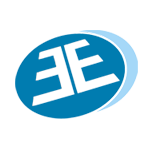
Multistrato
Multilayer, MLB sono i nomi che vengono utilizzati per identificare circuiti stampati Multistrato con ulteriori strati di piste interni.
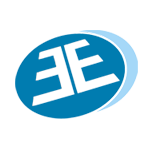
Solder
Solder resist o Solder Mask è chiamato lo strato protettivo normalmente verde che limita la saldatura alle sole piazzole e lascia scoperti anche i connettori a pettine e i contatti meccanici, viene spesso abbreviato in solder.